The Rise of Automotive Plastic Parts in Modern Manufacturing
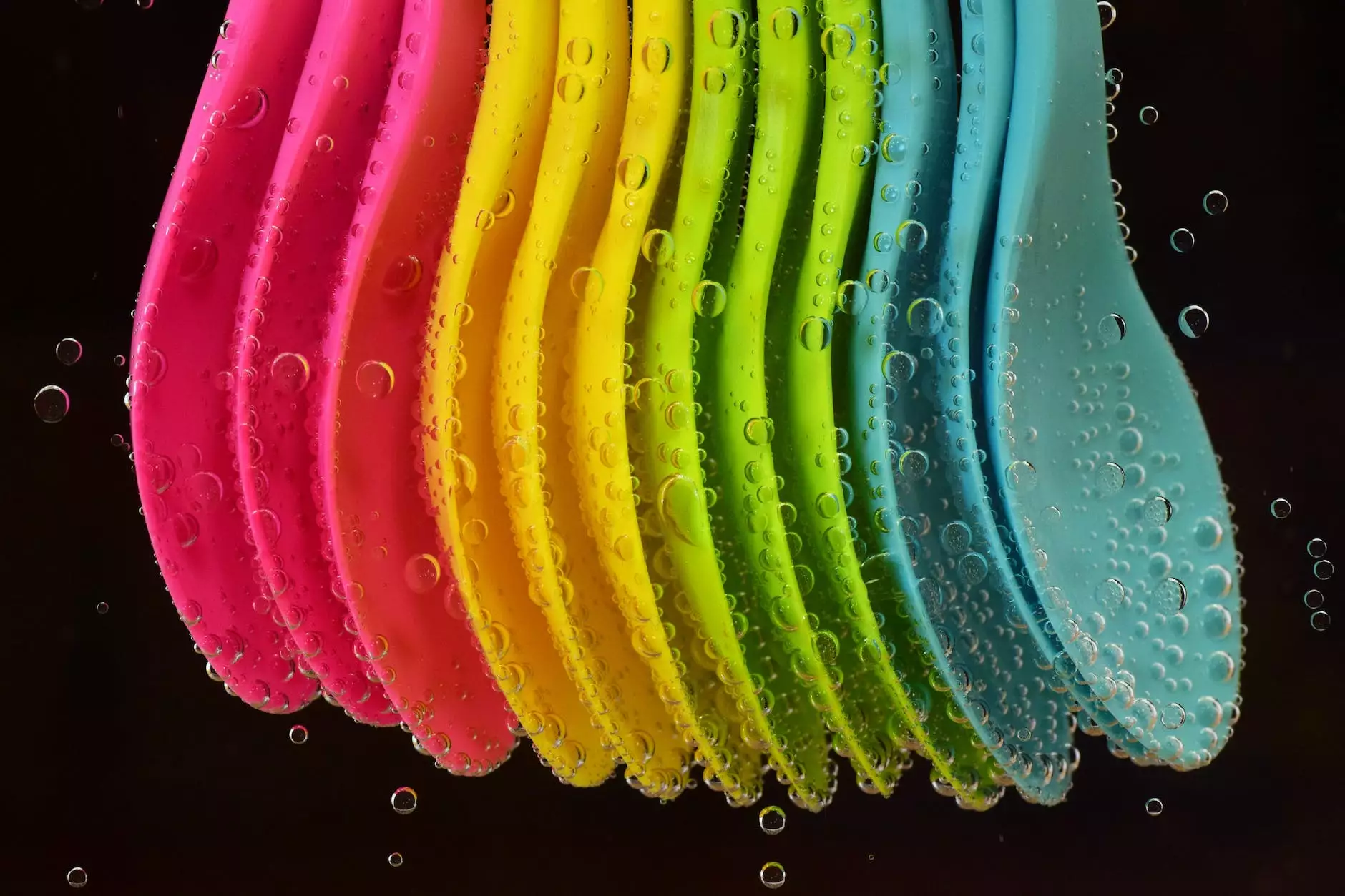
In today's rapidly evolving automotive industry, the automotive plastic part has emerged as a crucial player. With manufacturers constantly seeking innovative solutions to enhance vehicle performance, reduce weight, and improve fuel efficiency, the significance of these parts cannot be overstated. This article delves into the myriad benefits of automotive plastic parts, their applications, and their transformative impact on the industry.
Understanding Automotive Plastic Parts
Automotive plastic parts refer to components made from various types of plastic, which have been molded or shaped to fit specific automotive applications. These parts may include:
- Dashboard components
- Bumpers
- Interior trim pieces
- Exterior lighting fixtures
- Under-the-hood components
- Fuel tanks
The use of plastic in automotive manufacturing has grown significantly over the years. According to research, the average automobile contains approximately 50 to 70 pounds of plastic components, demonstrating the material's integral role in modern vehicle design.
Benefits of Using Automotive Plastic Parts
1. Weight Reduction
One of the most compelling advantages of automotive plastic parts is their ability to significantly reduce vehicle weight. This is crucial in the quest for improved fuel efficiency and reduced greenhouse gas emissions. For instance, substituting traditional metal components with plastic can lead to weight savings of up to 50% without compromising structural integrity.
2. Cost-Effectiveness
Manufacturing automotive plastic parts is often more cost-effective compared to their metal counterparts. The processes involved in producing plastic components, such as injection molding, allow for:
- Lower material costs
- Reduced labor costs
- Minimized waste during production
This combination of factors results in cheaper overall production costs, which can be passed on to consumers, making vehicles more affordable.
3. Design Flexibility
Plastics offer unparalleled design versatility, enabling manufacturers to create intricate and complex shapes that would be highly challenging or impossible using metal. This flexibility allows for enhanced aesthetic appeal and functionality, including:
- Textured surfaces for better grip
- LED integration in lighting fixtures
- Customizable colors and finishes
4. Resistance to Corrosion
Unlike metals, plastic parts are resistant to corrosion and rust, which can be critical in extending the lifespan of vehicle components exposed to the elements. For example, plastic fuel tanks and bumpers retain their integrity longer than metal parts, leading to reduced maintenance costs over time.
5. Improved Safety Features
The automotive plastic part industry has made significant strides in enhancing vehicle safety. Advanced plastics can absorb impact energy better than metal, which improves occupant protection during accidents. Innovative designs also allow for the integration of safety features, such as crumple zones and energy-absorbing structures.
Key Applications of Automotive Plastic Parts
1. Interior Components
The use of plastics in vehicle interiors has become standard practice. The lightweight nature, combined with design flexibility, allows for:
- Custom dashboards
- Comfortable seating supports
- Durable flooring and trim
2. Exterior Components
From bumpers to body panels, exterior plastic components have nearly replaced metal in many designs. The benefits of weight reduction and resistance to denting and corrosion make plastics ideal for:
- Car bumpers
- Fenders
- Hoods
3. Under-the-Hood Applications
Modern engines and electrical systems increasingly incorporate plastic components. These include:
- Engine covers
- Intake manifolds
- Cooling systems
These parts can withstand high temperatures while contributing to overall weight reduction, making them essential in engine design.
Challenges Facing the Automotive Plastic Parts Industry
While the benefits of automotive plastic parts are substantial, several challenges must be addressed to ensure continued growth and innovation in this sector:
- Recycling Concerns: Plastic waste is a growing ecological concern, prompting manufacturers to invest in sustainable practices, such as developing recyclable or bio-based plastics.
- Material Limitations: Certain plastics may not hold up well under extreme conditions, leading to potential failures in high-performance vehicles.
- Regulatory Challenges: As environmental regulations tighten, the industry must adapt to comply with new standards related to material composition and recyclability.
The Future of Automotive Plastic Parts
Looking ahead, the future of automotive plastic parts appears incredibly promising. With the push for electric vehicles (EVs) and advancements in manufacturing technologies, we can anticipate several exciting trends:
- Increased Adoption of Bioplastics: There is growing interest in utilizing sustainable materials that reduce environmental impact, making bioplastics an attractive option.
- Advanced Manufacturing Techniques: Innovations such as 3D printing and smart manufacturing are set to revolutionize the production processes for automotive plastic parts.
- Integration of Smart Technologies: Future vehicles may incorporate smart plastics capable of monitoring conditions or improving vehicle safety on their own. This includes sensors integrated into plastic parts that can relay information to the driver.
In conclusion, the automotive plastic part sector has become indispensable within the automotive industry, providing lightweight, cost-effective, and aesthetically pleasing solutions to modern manufacturing challenges. As technology advances and sustainability becomes more prominent, the role of plastics in automotive applications will only continue to grow. Businesses like DeepMould.net enable the production of cutting-edge plastic components, positioning themselves at the forefront of this innovative industry.
For manufacturers and consumers alike, embracing the advancements in automotive plastic part design and production is not just a trend—it's an essential step towards achieving a greener, more efficient, and safer automotive future.